In order to meet the growing demands of the market, various industries are turning to motion control. Motion control allows manufacturers to shift from manual to automated processes. It is used in printing, packaging, assembling, production, and textile industries.
This article will help you understand how motion control works and how to choose the best system that will work for you.
Types of Control Systems
There are three major types of industrial automation and robotics control system including PLC, PAC, and IPC that employ a different range of functionalities.
PLC
PLC is a classic yet versatile controller family that has been used for decades. It’s well-known for its flexible design of input-output configuration even though the form factors don’t vary. At this point, you can basically use PLC to control various applications. PLC commonly employs ladder logic programming customizable for a purpose of which the control system makes decisions on.
PAC
PAC is the PLC’s newer versions that still employ similar design and form factor but with some innovations. The controller captures the controlling designs appearing in mobile devices and Personal Computer (PC). The adaptations have enhanced capabilities of the PAC controller including broadened data-logging and communications for industrial automation applications. This second-generation controller has multiple programming options and is capable of controlling high-end applications.
IPC
IPC is an industrial controller that employs a more compact component design and operating system. The controller comes with rack mounting or DIN-rail and highest capabilities in terms of storage, communications, and processing power. The unstable operating system was an issue but newer version IPC is more stable now.
Comparing Different Motion Controllers
PLC, PAC, and IPC have differences mainly in controlled applications, capabilities, and communications.
Application Suitability
PLC is designed for and commonly used in machine control applications thanks to its small form factor, low-cost hardware, and simple programming. OEM machine builders make PLC as their main industrial automation and control controller option.
As the PLC’s second generation, PAC has widened the control applications by employing simple data logging that allows access to the controller’s data. At this point, PAC can specify all types of control applications, making it more flexible usage. On the other hand, IPC is designed and more suitable for process control applications with advanced control Proportional Integral Derivative(PID) that accommodate more complex projects.
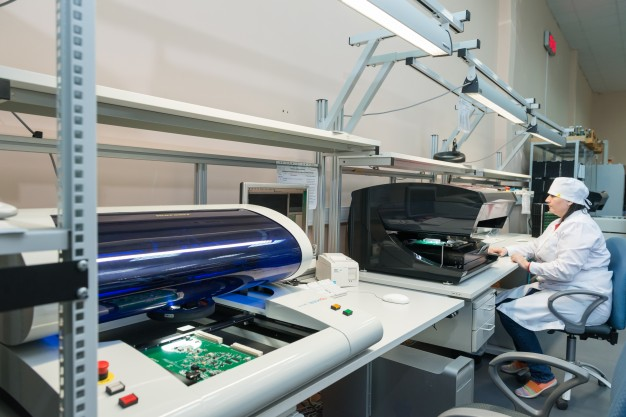
Capabilities
Capabilities of PLC and PAC for current industrial automation meet at some points while the gaps are narrowing. However, PAC has more enhanced data collection capabilities, expanded memory, and more various input-output format that basically make it more flexible than PAC.
PLC’s data collection capabilities are even more expanded and distributed along with the control application that makes it perfect for IPC plants.
Communication
While PLC can communicate well with machine control applications, PAC can control more than eight axes of motion and is able to communicate with smart vision sensors in real-time. PLC communicates to a central industrial PC(IPC) while employing modular skid systems distributed throughout the facility.
Factors to Consider When Choosing Motion Controllers
There are definitely some factors you should consider to choose the industrial automation devices for the applications you’d run in your facility. These include:
Compatibility: ensure the controller products compatible with the new or existing system.
Temperature Limits: Temperature limits of typical operating controllers range from 30°F to 130°F. Check the environment of your factory and if the temperature rises above the limits, choose tougher controllers.
Discrete Devices: List all discrete I/Os and mark up the total to 20% to create rooms for future expansion.

I/O Coverage: Ensure that controllers accommodate the types of I/O you’re using. Some controllers limit high-speed I/Os as well as some other analog and specialty inputs and/or outputs. List them all as your guide to buy the I/O.
Communication: Controllers should facilitate the communication you need including for programming or other systems. Ensure they have adequate communication ports and support protocols for your applications.
Input-Output Locations: List and map the local and remote I/O you need in the facility. The controller should accommodate the adequate communication protocols to cover those I/O needs
Programming: Ensure that the controller supports the program instructions for your application. You may consider the one with the PID loop function for specific applications. List down all programming functions required and ensure the controller supports them.
Conclusion
Choosing suitable controllers for each application is inevitable for industrial automation implementation. As you’ve seen above, each facility may require a different controller to use. Take these points as your guide in choosing the best controller for more effective operation in your own facility.