The employee’s waiting time is often known as Idle time. It can also be used to determine the processing time of a computer and the period when the machine isn’t in operation. For employees or machinery, idle time is regarded as an unpaid period. Every piece of machinery installed in your business has downtime at some point. In this case, downtime refers to the period that the machine can’t be utilized due to servicing or planner maintenance.
The machine or equipment is taken back to the repair center to be repaired. The downtime is inevitable. It’s considered a standard business practice, whether you operate either a manufacturing company or run a retail store. It is something that a business can’t manage. But, the company does have total control over any abnormal idle time. For instance, if an employee from your company strikes, that results in an abnormally long idle time.
What Is Idle Time?
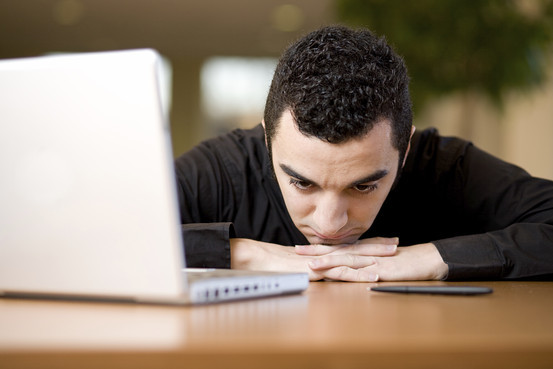
Idle times are when employees are receiving wages but aren’t productive because of a work interruption that could be due to various reasons. The reason could be a variety of reasons, and it may or may not be managed by the management. It can also mean the time that the machine isn’t running. In any situation, it’s a non-productive time. This means that the company is losing money due to the fact that they are still incurring expenses even though production has ceased. However, it should be noted that idle time cannot arise under method because all workers are hurry to complete their work. With that being said, every company will definitely want to eliminate idle time.
Types of Idle Time
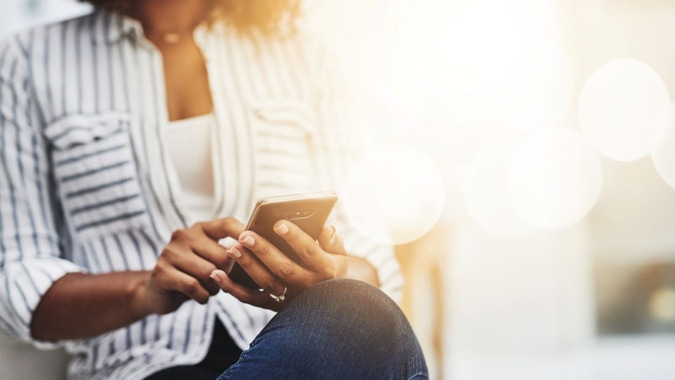
Normal Idle Time: Normal idle times are categorized by “downtime” for regular maintenance and repair. The regular maintenance and repair of manufacturing equipment is a standard routine and cannot be managed by management.
Abnormal Idle Time: Reasonable idle time, like an employee strike, is not normal and can be, in many instances, be managed by the management. Managing time is crucial in every business, especially when there are high fixed costs. Equipment that is not used creates depreciation costs and decreases output productivity.
The Formula for Calculating Idle Time
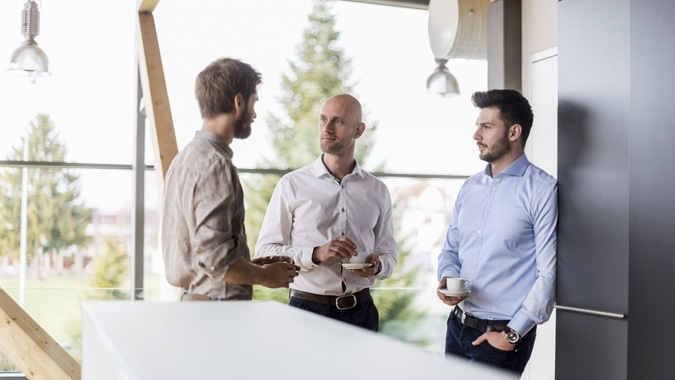
After we’ve looked over how idle times are defined, it’s time to look at the best calculation method. The formula to calculate idle time is:
Idle Time = Scheduled Production Time – Actual Production Time.
The term “scheduled production time” refers to the length of time managers plan to use special equipment over a given day or week, month, or even a year. Production time in actual terms is the duration of time the equipment runs in the way it was it was intended.
For instance, let’s say engineer clocks six hours of productive work in the course of an 8-hour shift on a Monday. It means he could work for an idle period of 2 hours. Also, the warehouse must use conveyor belts all day long. It takes 15 minutes to start and then another 15 minutes to close. In addition, the machine will be shut off for an hour in the course of a regular shift change.
In this case, the conveyor belt will typically be in operation through 8.5 hours of planned production every day. But, suppose the second shift operator is 1 hour late for begin work the following Monday. His delay will cause one hour of inactivity on the belt conveyor.
Examples of Idle Time
Vehicle Assembly
A car assembly plant produces 100 vehicles in an eight-hour workday. On certain days, quality testing and inspection teams will only take care of 50 cars during a shift. If this occurs, the assembly line stays inactive until the facility’s quality inspection team can catch up.
Shipping Containers
A shipping company is affected by delays in its delivery at the port due to a storm that has hit the sea. Therefore, their transportation system is idle until calmer waters are restored. Once calmer, workers can shift containers on the ship as scheduled.
Software Development
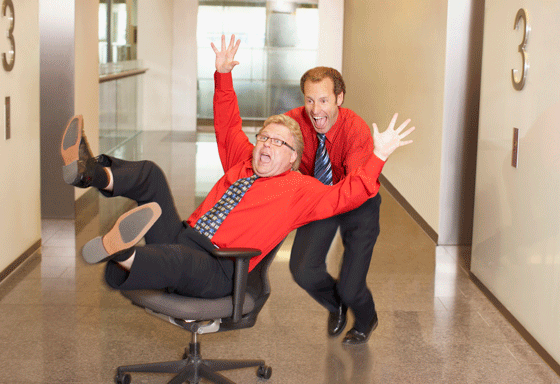
Software development involves a team of individuals with varying specialties–user-experience designers, user-interface designers, front- and back-end developers, and full-stack developers–working toward the goal of building an application for a client.
In this case, some workers may have breaks, causing idle time, while some are more productive. Data dependence can lead to an employee not performing their work while another works on the task.
Tips to Boost Productivity Levels and Reduce Idle Time
Workflow Optimization
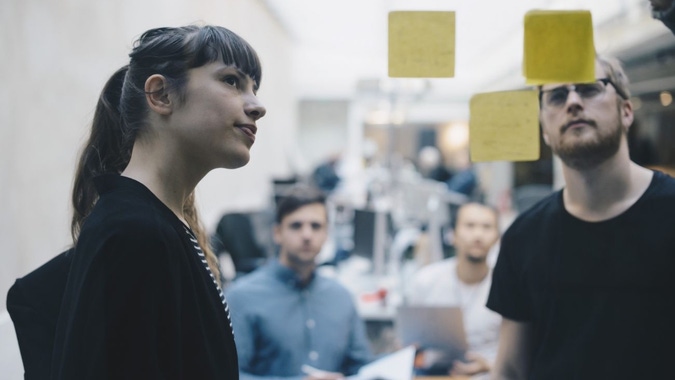
Inefficiencies in workflows and processes are a common cause of idle time. Therefore, identifying the causes and removing them as early as possible can improve productivity.
To reduce an employee’s idle time, create a more balanced schedule. Also, you can try getting rid of administrative duties that are not needed and ensuring that employees have the appropriate equipment.
When it comes to optimizing the machine, make sure that the machines are arranged so that the output from one machine is effectively connected to the input of the other. Additionally, ensure that there is enough labor available to run the machines.
Keeping Equipment in Good Condition
Equipment that isn’t operating at its best is also a cause of inefficient time. Studies have shown that the return on investment of implementing a regular preventive maintenance program is very high. The cost of identifying issues in the early stages is less than the costs of a breakdown, idle period, and downtime. When replacing components of the machine, stay away from parts that aren’t of the highest quality and choose OEM-approved parts. Finally, to ensure that maintenance is completed in accordance with the schedule and that all checklists are correctly executed, make use of CMMS software.
Final Words
idle time occurs when assets and people aren’t working, even though they could be. It’s distinct from downtime, which refers to the time when your assets aren’t productive, either due to planned maintenance or because of an unexpected malfunction. It’s not possible to stop idle time, but you can do your best to cut it down.