2020 has brought a lot of disruption to the average supply chain, from COVID-19 to concerns about Brexit. Now more than ever, businesses need to balance resilience and efficiency to secure their networks. Whether your business is e-commerce or physical, you need a reliable supply chain. In many cases, more resilience means higher costs, but the cost of doing nothing will be even higher. Here’s how to build a more resilient supply chain.
Inventory and Capacity Buffers
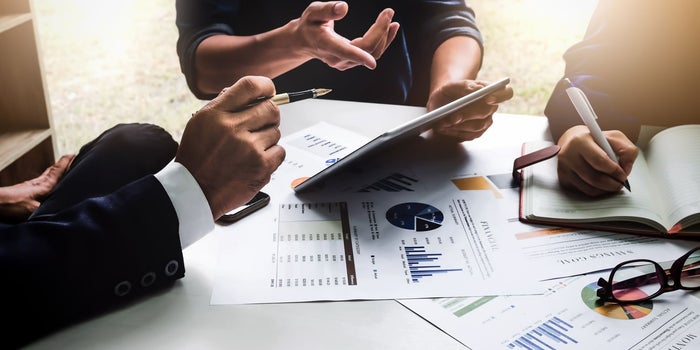
Buffer capacity is the simplest way to boost resilience, whether in the form of underused production facilities, or inventory in excess of safety stock requirements. Buffers are expensive, making this a challenge, and supply chain leaders can find it hard to justify them.
Leading companies, like Source Engine, will use buffers in the form of surge capacity for new product launches, or expansions into new areas of growth. You can also create buffer capacity by using contract manufacturers strategically for your surge needs.
Manufacturing Network Diversification
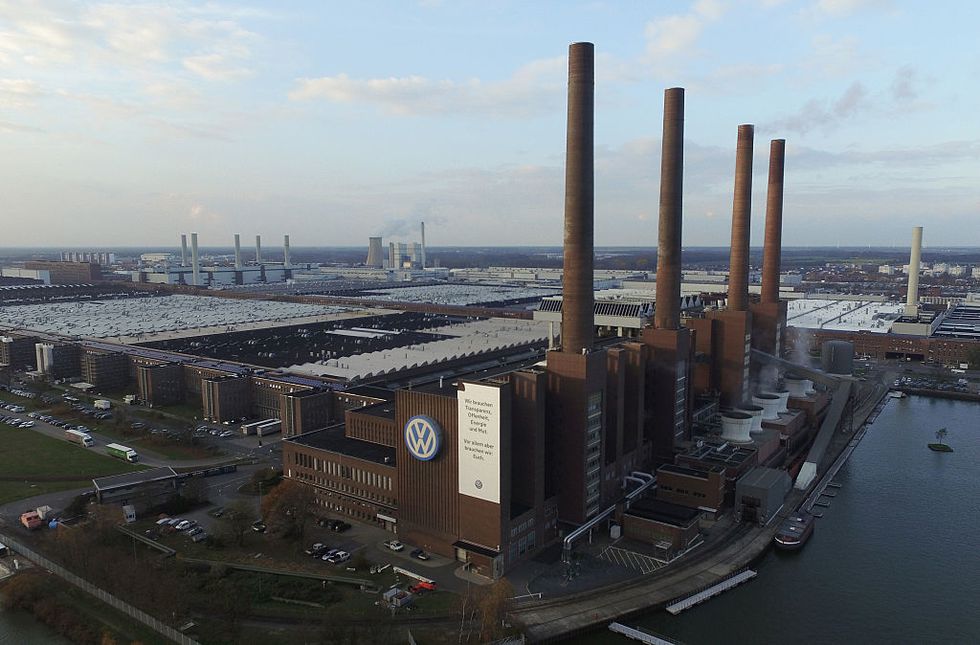
Many companies have recently begun to diversify their sourcing or manufacturing bases, partly due to the US-China trade war. This has, in some cases, meant switching to new suppliers outside China or asking existing parters to supply from elsewhere in Asia, or from new places, like Mexico.
Disruptions to supply chains have increased over the last few years. This means that you should view the cost of keeping multiple supply locations as the cost of doing business, not an inefficiency.
Multisourcing
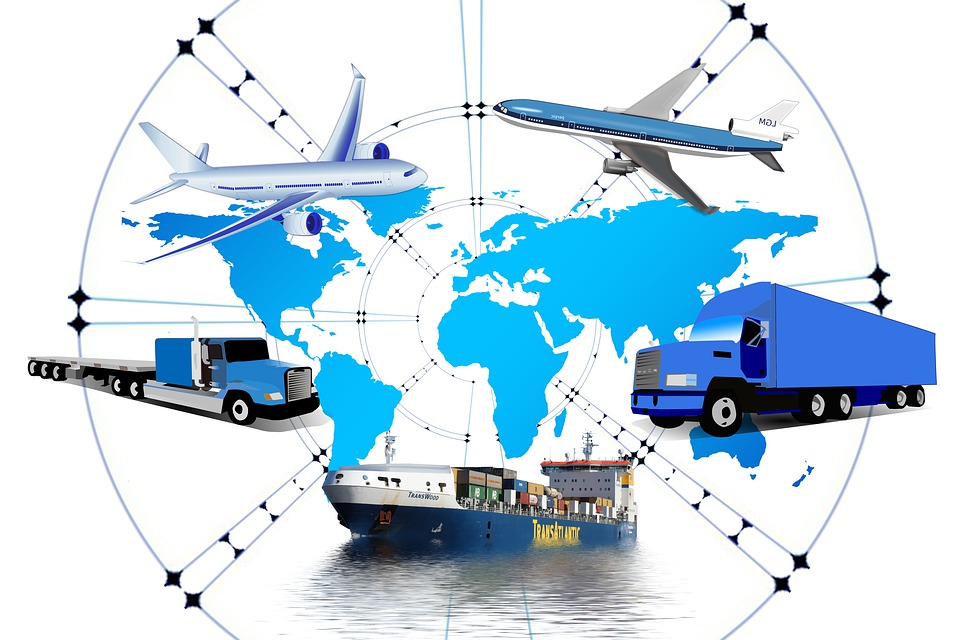
A good example of why you shouldn’t rely on one source is the 2011 major natural disasters in Japan and Thailand. Supply chains across the world were hit. In the automotive industry, for example, cars that were almost finished could not be shipped to customers, due to missing components. Multisourcing mitigates the risk of this happening.
To build a multisourcing strategy, supply chain leaders must know their supplier networks in great detail and be able to categorize suppliers by spend and by revenue impact if a disruption were to occur. Award businesses to additional suppliers, or work with an existing single or sole-source supplier that can produce from multiple locations.
Nearshoring
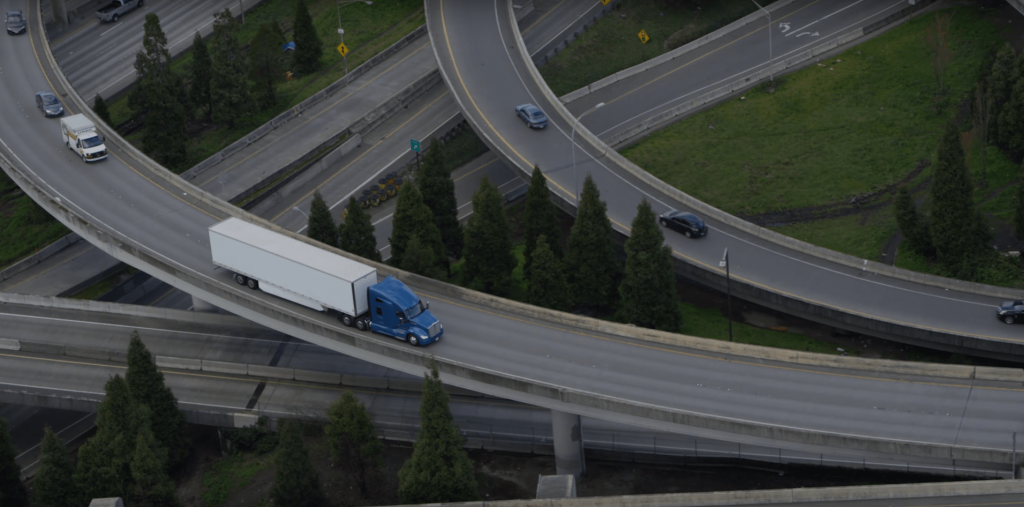
Some companies want to reduce geographic dependence in their global networks and shorten cycle times for finished products. Regional or local supply chains can be more expensive, because they add more players and complexity to the ecosystem, and allow for more control over your inventory levels.
Platform, Product, or Plant Harmonization
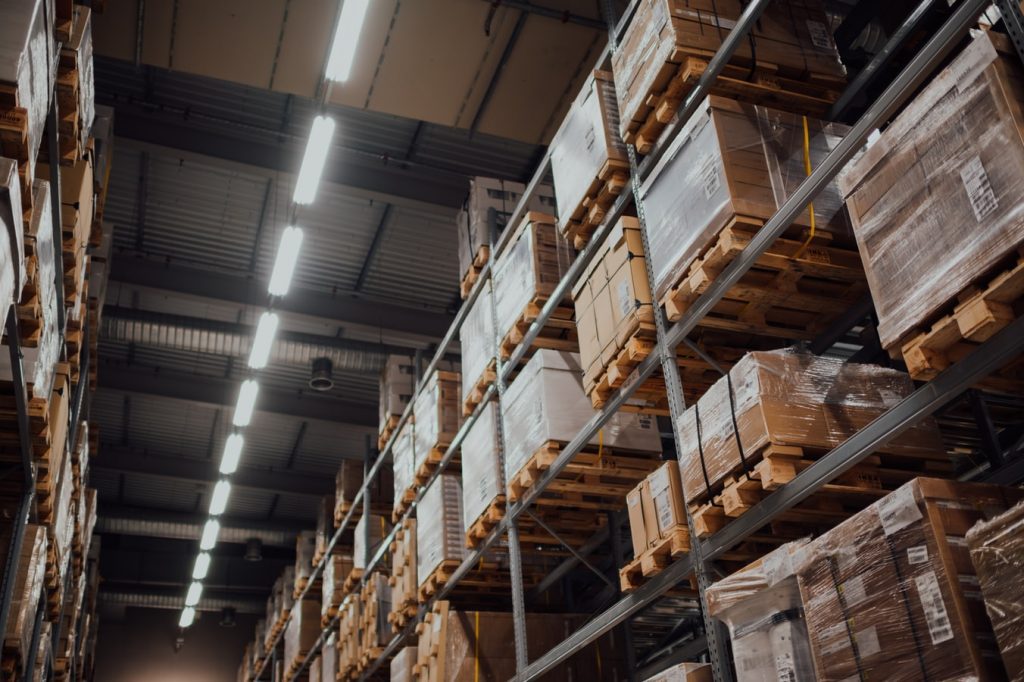
The more regionalized your network is, the more harmonized your plant technology has to be in order to allow products to move easily across the network. A good example of this harmonization is the use of the same vehicle platforms for a range of models in the automotive industry.
Standardizing components across multiple products, especially ones that aren’t important to and will never be seen by the customer, is another form of harmonization. This makes sourcing policies simpler and creates more opportunities to place higher volumes among multiple suppliers, increasing resiliency.